金属3D打印已成为义齿加工厂的常规加工方式,设备,材料,人力构成了加工成本的主要组成,其中材料成本占据了最终牙冠或支架的大部分成本,因此金属粉末的利用率是影响到最终成本的一个重要因素。粉末利用率的计算公式=成型义齿产品重量(冠或支架去支撑后)/粉末投入总量,粉末利用率的高低直接影响到最终成本。
最终成型的义齿的重量是固定的,那损耗的粉末都去哪里了呢?
主要有以下几个环节:
1. 打印产品的支撑结构耗粉
2. 打印过程中被风场带走的粉尘(进入循环过滤系统和集尘罐)
3. 打印完成后的清理取件环节损耗粉末(如被吸尘器吸走等)
4. 打印完成后的粉末重新筛分环节分离的筛网残留粉
因此如何降低以上4个过程的粉末损耗成为提升粉末利用率的关键。
今天我们先来介绍一下如何提升第4个环节打印完成后的粉末重新筛分环节粉末利用率。
在3D打印过程中,不可避免会有粗粉末颗粒的产生,利用高品质的粉末可以降低产生的机率但不能避免(高品质粉末本身粒径小且均匀),所以需要通过筛分工艺,将粗粉末颗粒筛除,进而获得满足3D打印要求的金属粉末,保证产品稳定性。
影响筛分的几个重要因素:
1. 筛网干净通透,无堵塞情况
2. 筛网合适规格
3. 合适的筛分工艺
一、筛网为什么会堵塞,如何避免堵塞,堵塞后如何清理?
a) 为什么会堵塞,堵塞后产生什么影响?
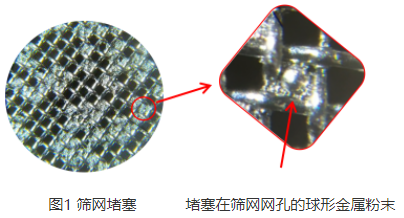
将打印完成后的金属粉末置于振动筛分机中,如果没有超声功能或超声功能未打开,筛分一次就会发现筛网被粗颗粒堵塞,通过光学物镜观察,如图1所示,约70%的筛网网孔出现堵塞,进而造成过筛的粉末重量减少,影响筛分得粉率。通过称重,筛分前原重量18.02kg,筛上粉末重量0.9kg,筛下粉末重量17.12kg,得粉率为95.01% 。接着对筛上粉末进行粒径测试,粉末的粒径数值为:D10:15.7μm,D50:31.2μm,D90:51.2μm,说明筛上粉末中的绝大部分粉末还可以接着使用。
b) 如何避免筛分过程中筛网的堵塞情况
在筛分过程中,对筛框增加超声波功能,如图2所示,可以有效防止筛网堵塞情况,经测试,经过10次筛分后 ,筛网依然保持良好状态,如图3所示。
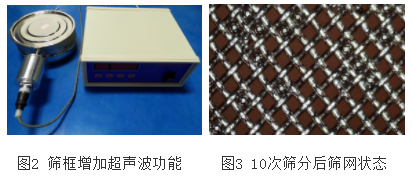
c) 堵塞后如何清理
即使加了超声功能也未必能保证筛网一直不堵塞,所以建议使用10次后对筛网用显微镜定期 观测,堵塞面积>30%时必须进行清理 ,如图4所示为用显微镜观测的过程。
德普润分别采用了物理振动,气枪吹和超声清洗对堵塞筛网清理,经过试验发现只有超声清洗是最有效的去除堵塞的手段。
在堵塞后,对堵塞的筛框进行超声清洗,超声清洗时间:15min,温度:35℃,超声清洗后,通过显微镜观察,筛网网孔的堵塞约为7%,堵塞情况明显改善,如图5所示。

清洗到什么标准才算合格呢,超声清洗也不会将堵塞100%消除,经过我们测试,只要筛网的堵塞面积<10%即可正常筛分。
二、筛网孔径的选择
筛网孔径太大会导致粗粉末难以被筛除,影响打印效果,太小又会导致细粉末被筛除,造成粉末浪费。
德普润分别对63μm,75μm和80μm孔径筛网进行了测试,对过筛后的粉末进行粒径测试,测试结果如表2所示,80μm筛网过筛后的金属粉末可以满足3D打印用金属粉末的粒径要求(粉末粒径10-53μm),63μm和75μm过于严苛,会导致部分可用粉也被筛除。
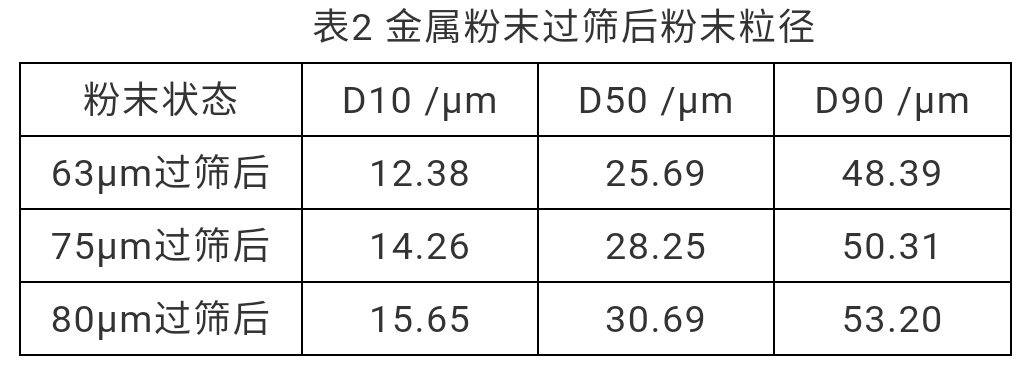
三、合适的筛分工艺
筛分可以调节的工艺有时间,加粉量和超声功率几个选项。针对每个筛分设备不尽相同,我们只能针对德普润自己使用的筛分设备给出最佳工艺,仅供大家参考:
每次筛分量≤3kg,筛分时间=3分钟,超声功率=C1档(电流约0.2A)
结语
1. 在筛分过程中,保证筛网干净通透,无堵塞情况(经测试筛网堵塞面积<10%即可),可通过采用显微镜定期观察,定期超声波清洗方式进行清理;
2. 选择合适筛网规格,80μm筛网即可;
3. 筛分环节:必须在筛框上增加超声波,建议每次投粉量3kg,筛分3分钟,超声功率=C1档(电流约0.2A)。
关于作者王庄:王庄于2015年毕业于北京工业大学材料科学与工程学院,获硕士研究生学位。从事3D打印金属粉末行业多年,技术理论扎实,并在医疗器械质量体系和产品注册方面拥有丰富的经验,目前就职于北京德普润新材料科技有限公司,任总经理助理。